PROCESS Consulting
Shape optimised business processes, reduce frictional losses and increase efficiency
PROCESS OPTIMISATION
Shape optimised business processes, reduce frictional losses and increase efficiency
Our processes consultants work hand-in-hand with ACOPA’s traditional IT business. Our consultants concentrate on optimising processes before they are digitalised.
We can create a custom solution that perfectly meets your needs using our expertise gained over more than 20 years of providing consulting services to DAX companies. The focus here is on ensuring optimum coverage of your process requirements, perfect integration into your existing system environment and the quality of offered software solutions (range of functions, user-friendliness, relevance etc.)
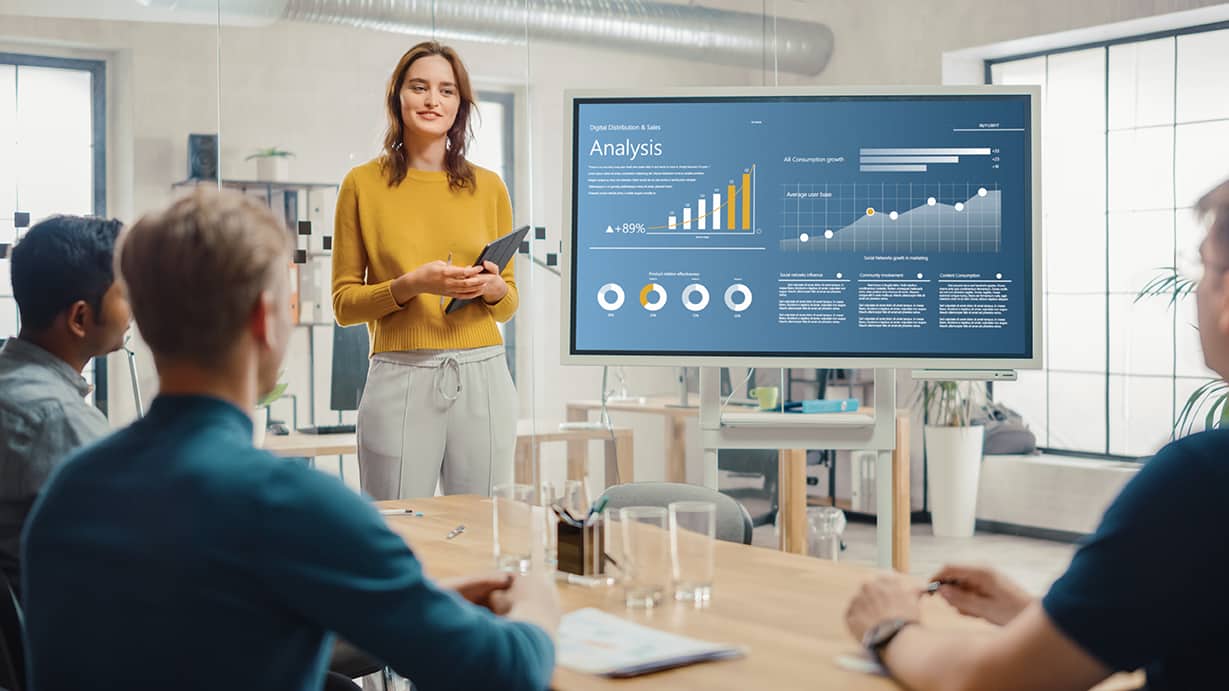
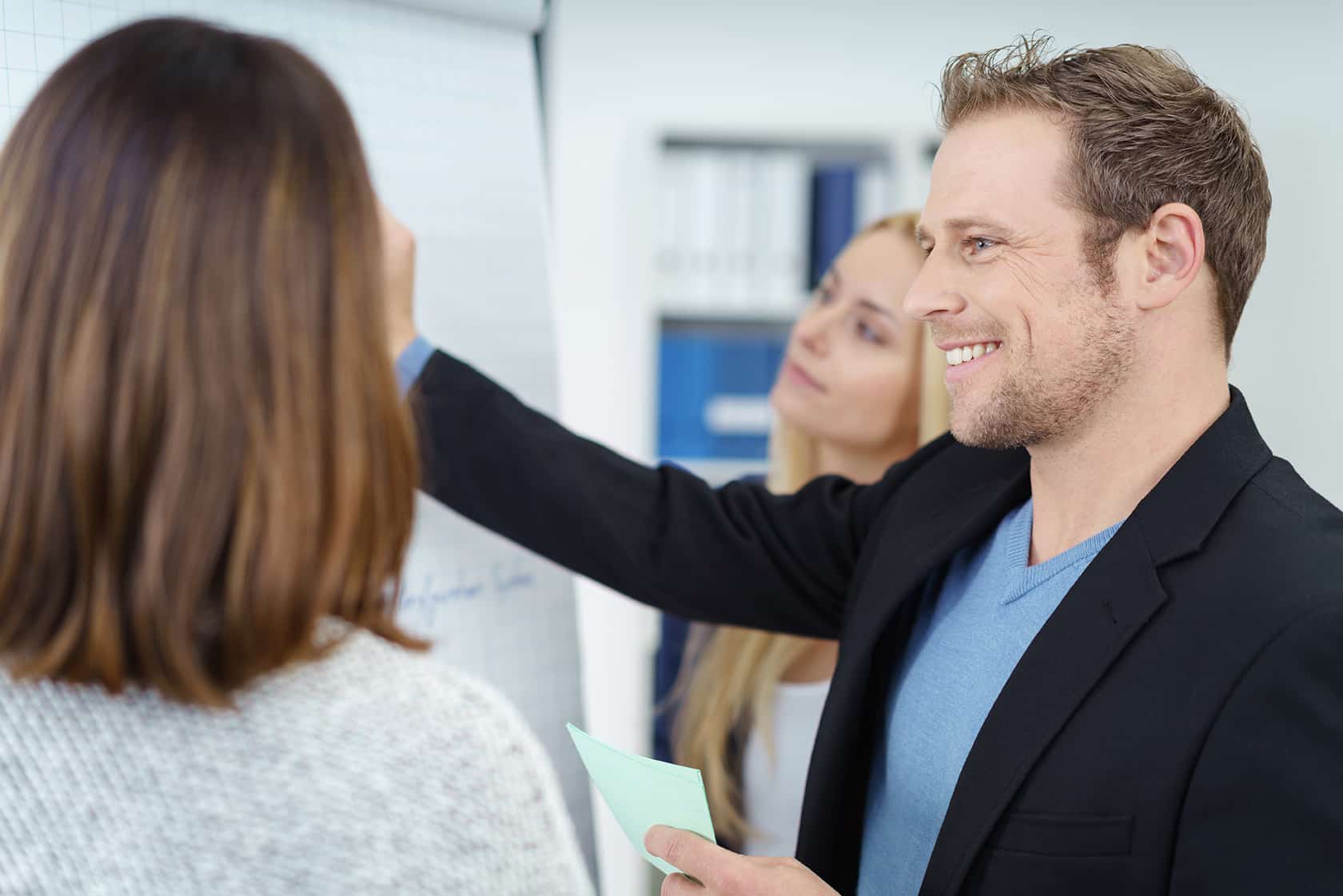
We primarily use lean management and SixSigma methods to ensure process excellence. We naturally also use digital Industry 4.0 tools, starting with paperless process management through to reporting tools and data-based performance dialogues with electronic task monitoring.
We can support you throughout the entire process, from implementation to roll-out, onboarding and staff training; everything revolves around ensuring maximum benefit for your company.
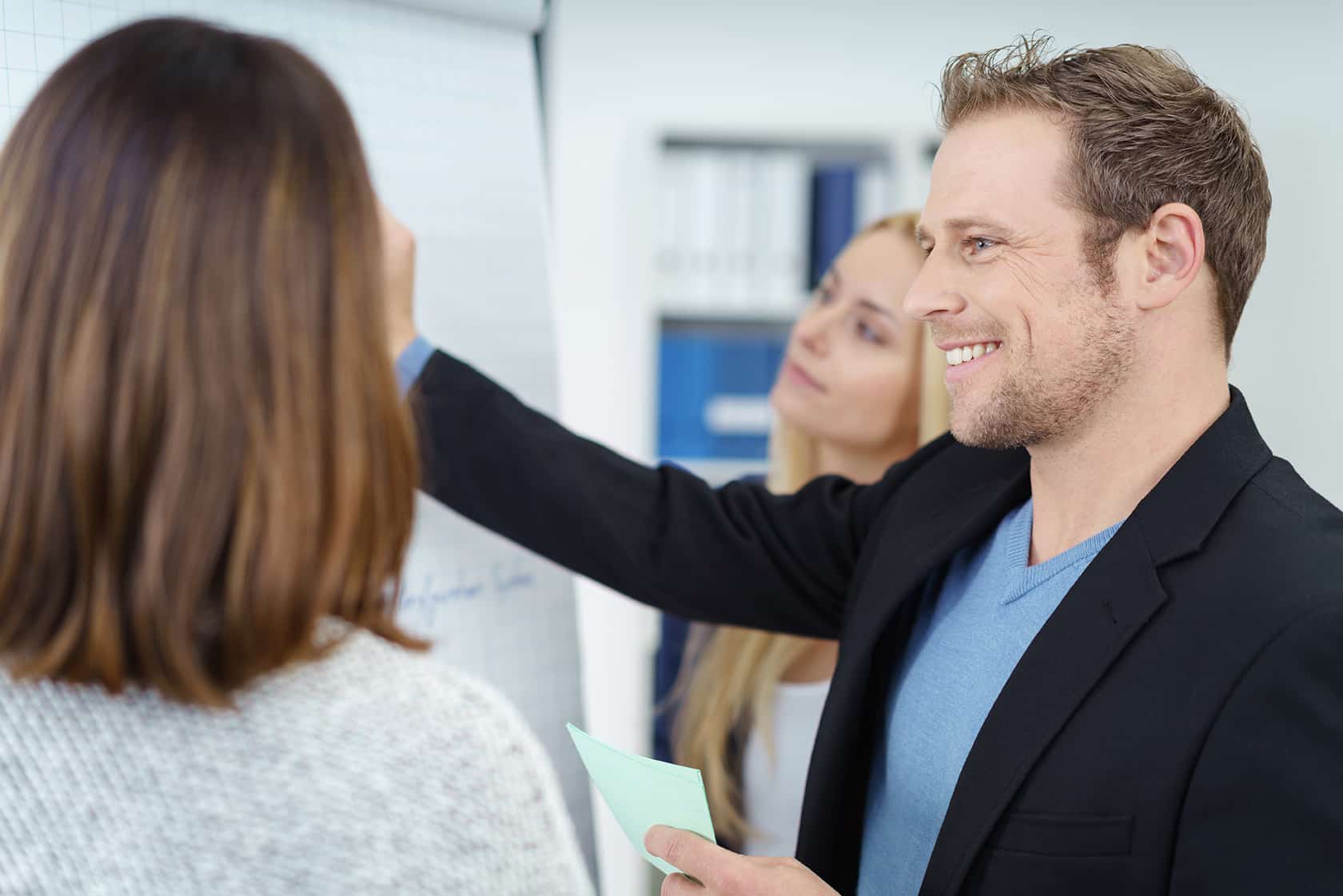
LEAN
The term lean management describes the entirety of the principles, methods and approaches used for efficiently shaping the entire value chain for industrial goods.
Lean management means creating value without waste. The aim is to optimally coordinate all activities necessary for value creation and avoid any unnecessary activities (waste or muda in Japanese).
Stable processes are the foundation of high-quality products that fulfil customer expectations. These stable processes are based on precise process definitions and interface descriptions, clear responsibilities, prompt responses to faults and simple methods of organisation.
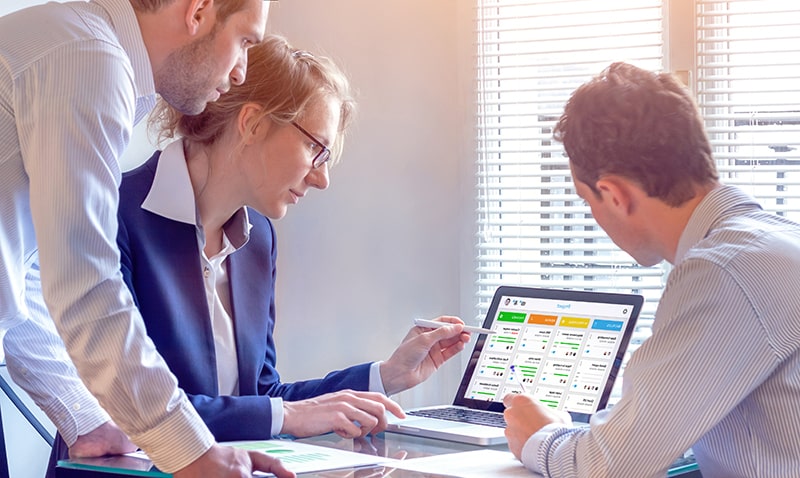
SIX SIGMA
Six Sigma is a management system for improving processes and also a quality management method. This method focusses on monitoring business processes using statistical tools. To do so, it uses a comprehensive set of tools for the systematic improvement or reshaping of processes.
The structure of a process improvement project is planned using the DMAIC method: Define – Measure – Analyse – Improve – Control. The ultimate aim of Six Sigma projects is to improve business results.
Lean management and Six Sigma can also be used in combination and supplemented with additional methods (e.g. Kaizen ). We would be happy to advise you on possible applications and how best to use them in your organisation.